Real story behind the development of a product 1
A moving industrial furnace!
Development of an Innovative Energy-saving Conveying System
In the early 1980s, against the backdrop of the high economic growth period of mass production and mass consumption, the industrial trend was toward heavier and heavier products, and the reaction towers (reactors) and tankers in scientific plants became larger and larger one after another. In line with this trend, parts and products to be heat-treated also became larger and heavier, and facilities capable of processing 1,000-ton-class products were required instead of the several hundred-ton class that had been used in the past.
Here is an example of one of our world-first innovations in this era.
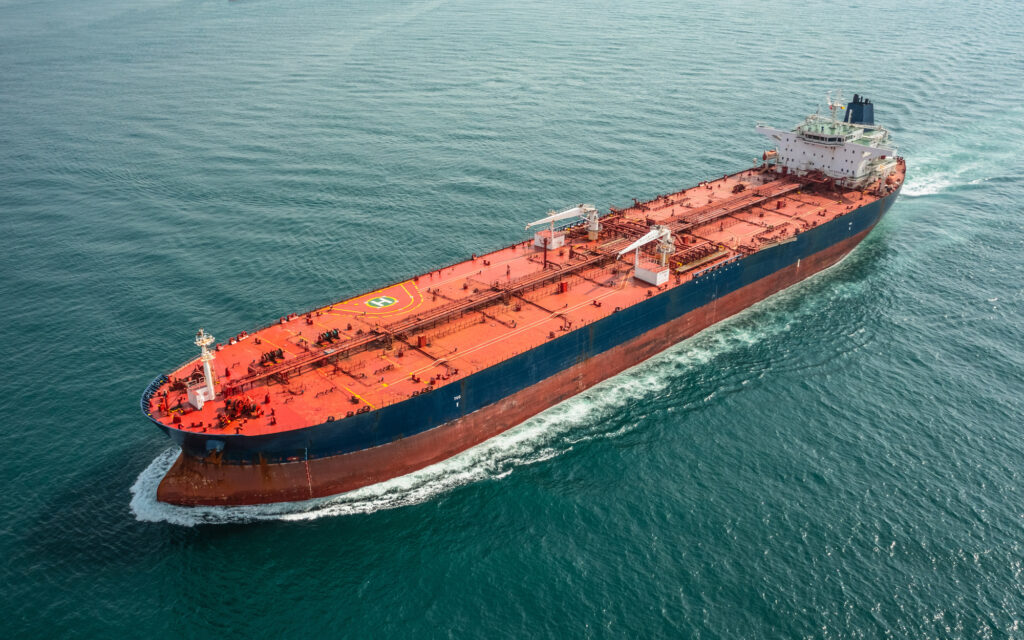
Character
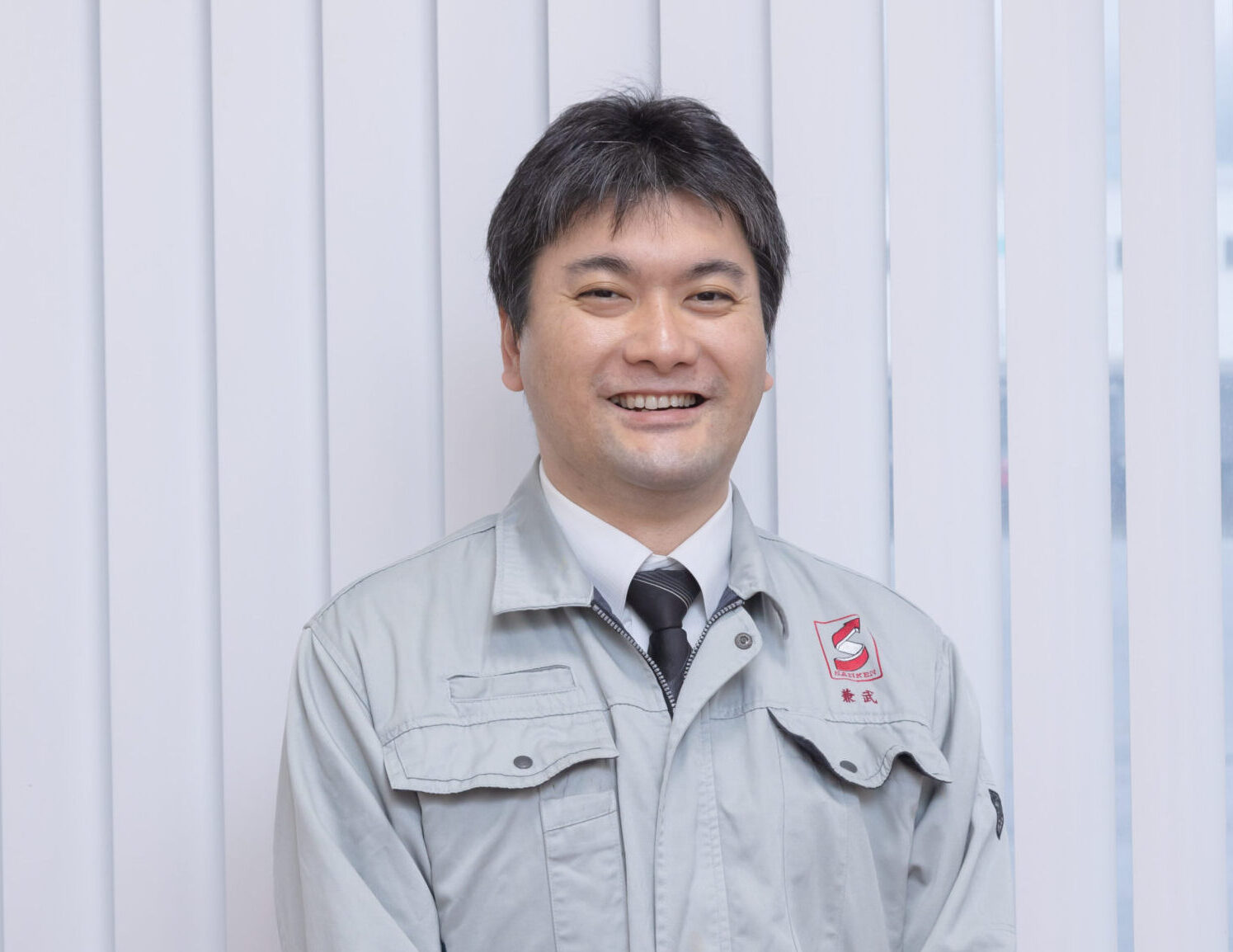
Senior Engineer:Mr. K
A mid-level engineer who joined the company in 2006. Since joining the company, he has devoted himself to designing steel-related industrial furnaces.
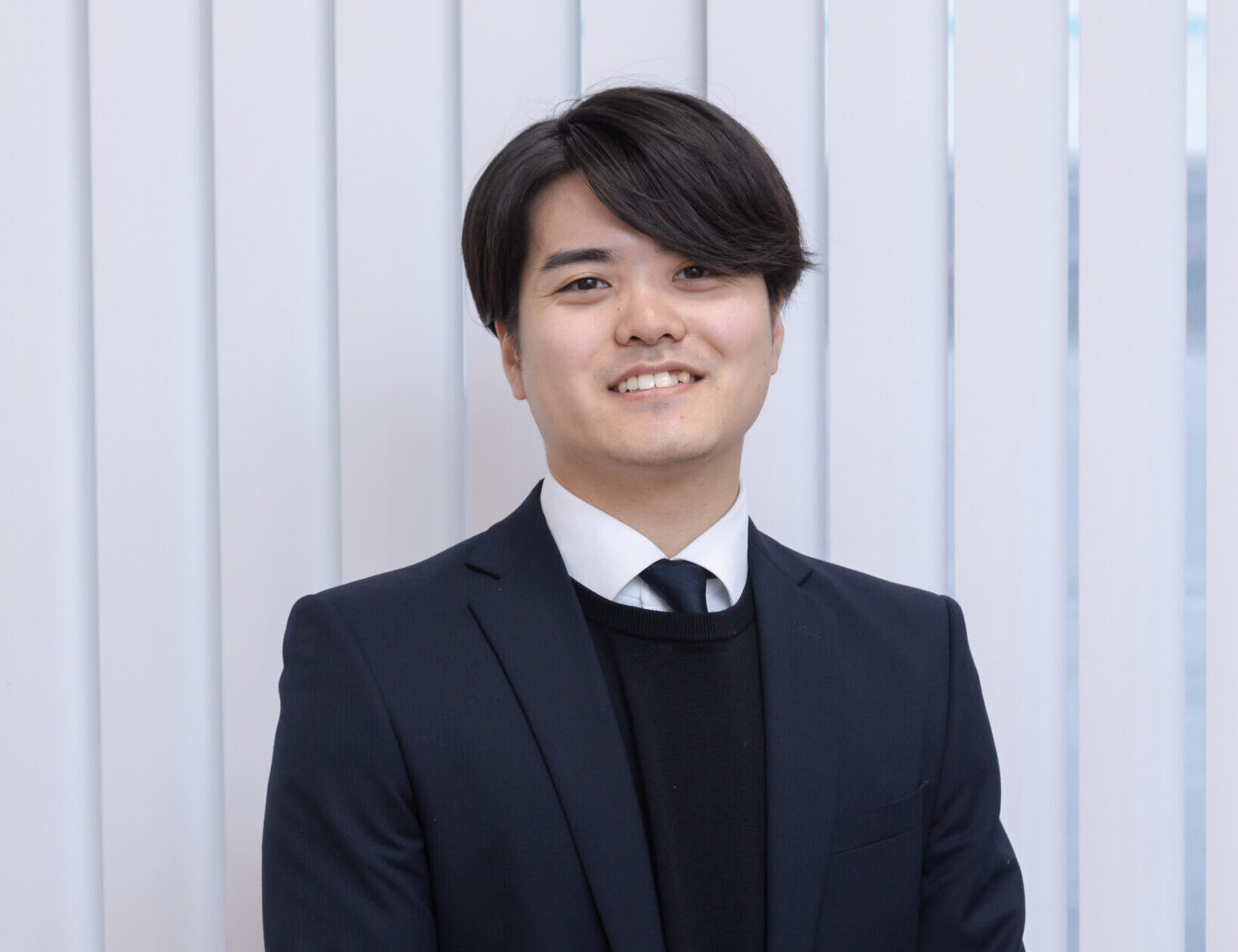
Young employee:Mr. H
A young sales representative who joined the company in 2022. His knowledge of industrial furnaces is still limited, but he is gradually learning the know-how through maintenance and sales work.
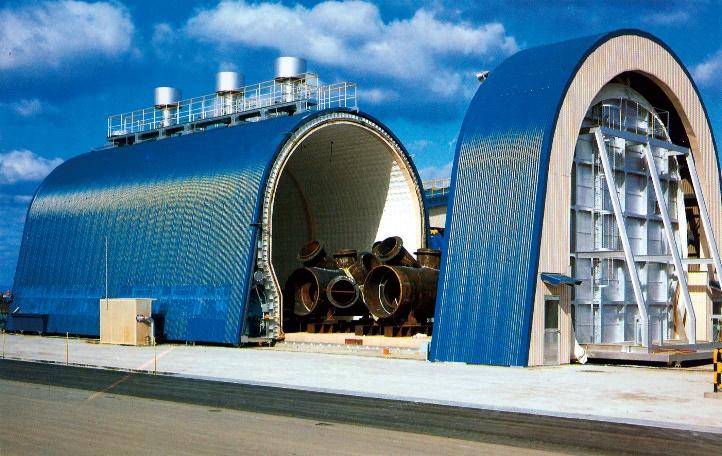
Mobile Furnace Body Type Heat Treatment Furnace
Heat treatment is performed by moving the equipment instead of the product and setting the product in the furnace. Energy consumption during heat treatment of large products can be reduced.
Equipment Born in the Era of Mass Production
Mr. H:
Nice to meet you today.
Mr. K:
Nice to meet you. Please ask me anything today so that you can explain our products well to your customers.
Mr. H:
Recently, we received an inquiry from a customer about a furnace with a movable body for heat treatment. This is an industrial furnace with a moving furnace body, which is a system that has never been seen before.
Mr. K:
The first furnace was developed in the early 1980s, before I was born, during a period of rapid economic growth, when plants and ships were becoming larger and larger for mass production and mass consumption. Naturally, products to be processed in industrial furnaces, such as rotor shafts for ships and pressure vessels for reactors, also became larger and larger, and it was often difficult to process them using conventional cart-type equipment, which led to the development of a body movabble type furnace.
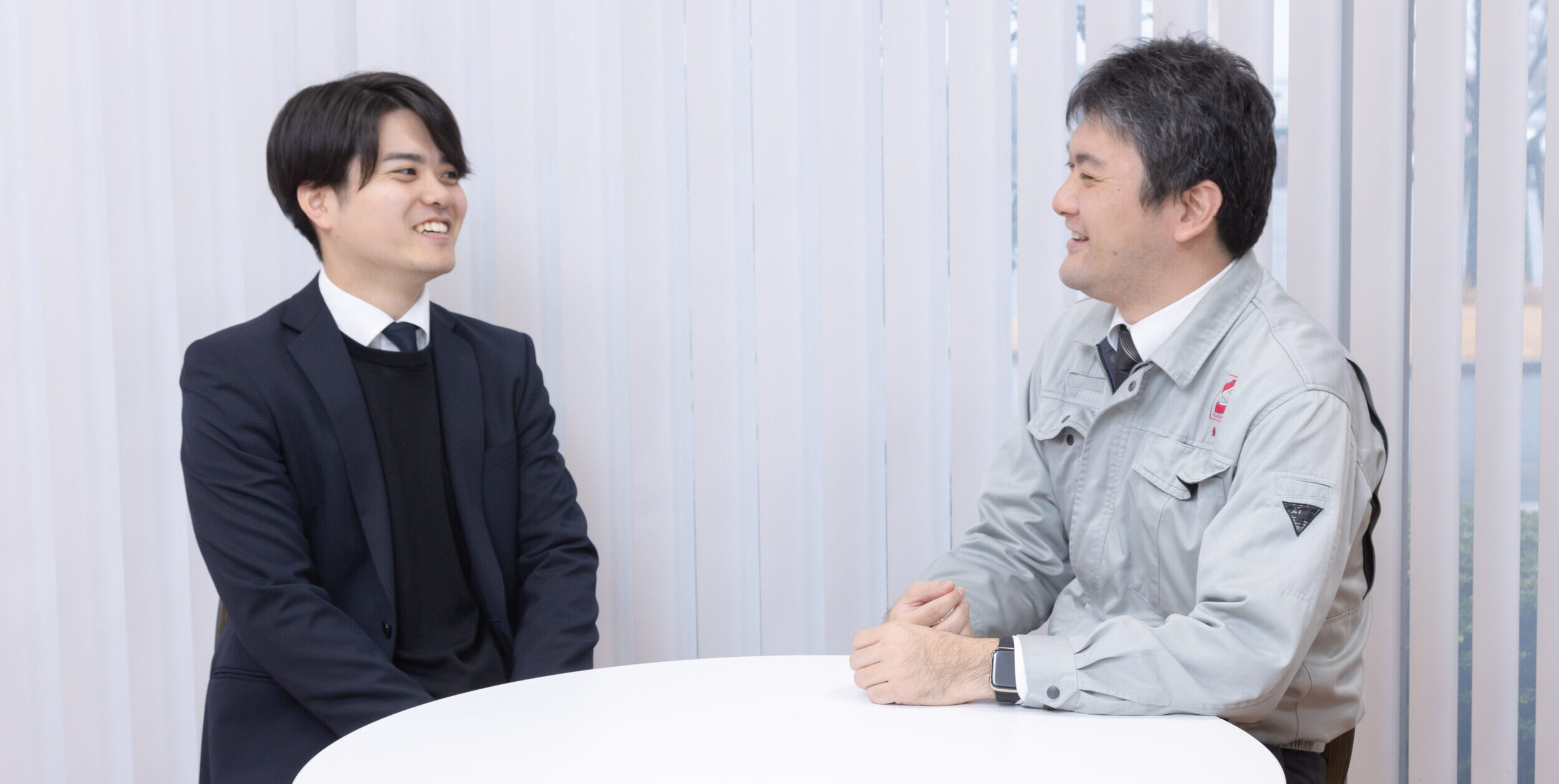
Heat treatment facilities for super-heavy products are expensive for foundation work.
Mr. H:
I see. I had thought that batch-type heat treatment furnaces for steel were generally of the cart type. What specific problems did you encounter when heat-treating super-heavy products?
Mr. K:
For large products, the weight exceeds 1,000 tons, so with the cart type as Mr. H mentioned, the foundation work would be very expensive to support such a heavy product plus the cart.
Mr. H:
I understood. Were there other methods other than the trolley type at that time?
Mr. K:
For example, when heat-treating a product several tens of meters long, such as a ship’s turbine rotor, a cart-type furnace would cause distortion of the product, so we dug a pit (hole) more than 20 meters underground and installed a vertical furnace for heat-treatment. However, this method also had the disadvantage that the foundation work, including the pit, was very expensive.
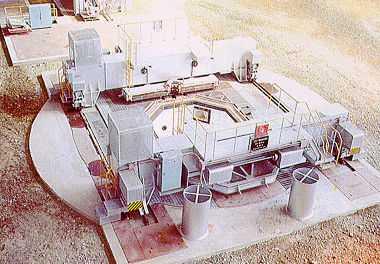
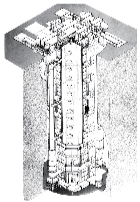
We solved the problem by reversing the idea of moving the furnace body instead of the product!
Mr. K:
That’s why we decided to build a facility that moves the furnace body to drastically reduce the cost of foundation work. Since the products are not moved, distortion is less likely to occur during heat treatment of long parts, and we were able to solve the problems of both the cart-type and pit-type furnaces.
The work of loading the processed products can also be done at the floor level, which reduces safety risks such as falling or tripping.
Mr. H:
I see, so the mobile furnace body type heat treatment furnace was born to solve the problems of the cart type and pit type. However, you said that the cart-type furnace had problems because the products weigh 1,000 tons, and I think the furnace body is also heavy…
Mr. K:
Sanken Sangyo’s heat treatment furnaces have been using ceramic fiber as a refractory material since 1969, and the benefit of this was that the weight of the furnace body was relatively small. For example, if a product weighs 1,000 tons, the furnace body weighs about 100 tons. Then, it would be much cheaper to move the furnace body, the cost of the ground foundation work would be much lower, and the energy required to move it would be only one-tenth of the cost.
Mr. H:
Yes, that is true.
By the way, If you didn’t have such an idea at the time, there must have been a lot of opposition.
Mr. K:
Of course, it seems that there were only objections from within the company and from customers. However, the engineer at that time went around and persuaded all the parties concerned, and the world’s first furnace body moving type heat treatment furnace was born.
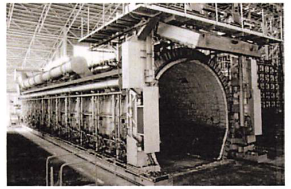
Long-selling products loved by customers
Mr. H:
The mobile furnace body heat treatment furnace is a product that became a hit by combining the novel idea of moving the furnace body instead of the product with the efforts of engineers who believed that it would be a success, isn’t it?
Mr. K:
That’s right. It is also a long-selling product, with about 50 units delivered to date, while making numerous improvements.
This system is attracting even more attention due to recent work style reforms, as it can improve productivity by allowing the next product to be heated at the same time as one product is being heated.
Mr. H:
Indeed, we still receive inquiries from customers more than 40 years after its development. Now that we know how it was developed, I will be able to communicate its features and benefits more clearly to our customers! Thank you very much.
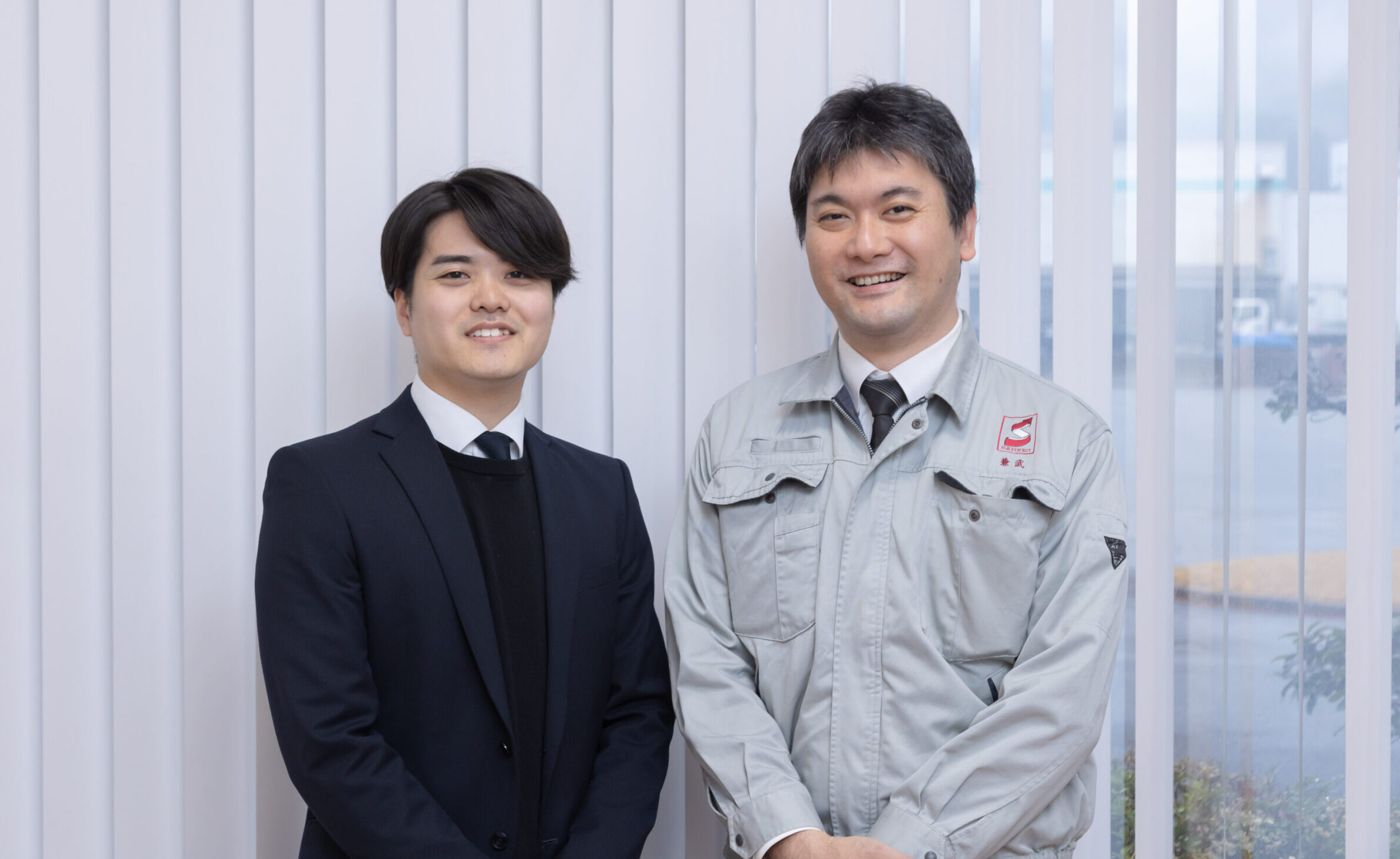