Features
High Safety
Molten metal is discharged at the touch of a button, without the use of a tap, allowing the operator to safely perform the metal discharging operation.
Low Cost
Compared to general tap molten metal dispensing, the cost of tap cones is unnecessary. Also, compared to other electromagnetic pumps and vacuum molten metal dispensers, there are fewer consumables and installation costs for replacement, greatly reducing running costs.
Tapped hot water supply | KAMAGAWA 2.0 | General pump | Vacuum suction hot water supply | ||
Initial Cost | Pump unit cost | ◎ | ○ | △ | ☓ |
Open well modification cost | ◎ | ○ | ☓ | △ | |
Running cost | Consumables cost | ◎ (Tap cone) | ◎ (Shaft, impeller, sleeve) | ☓ (Riser pipe and others) | ☓ (Pipes, packing, ladle) |
Maintenance cost | ☓ (Replacement of tap bricks, consecutive holidays work required) | ◎ (Replacement of consumable parts) | △ (Maintenance of pumps and pipes) | △ (Pipe maintenance) |
Automation and Quality Improvement
When combined with our original continuous launder type molten metal distribution system “Almap,” a series of operations from pouring to distribution can be automated. This eliminates the need for the conventional ladle distribution operation and improves molten metal quality by eliminating air entrapment in the molten metal due to receiving and supplying (turbulence) molten metal. In addition, the system has various advantages such as eliminating the time required for waiting for the ladle to be dispensed, enabling continuous operation, and ensuring that the level of molten metal in the holding furnace is constant, so that casting can always be done under the same conditions.
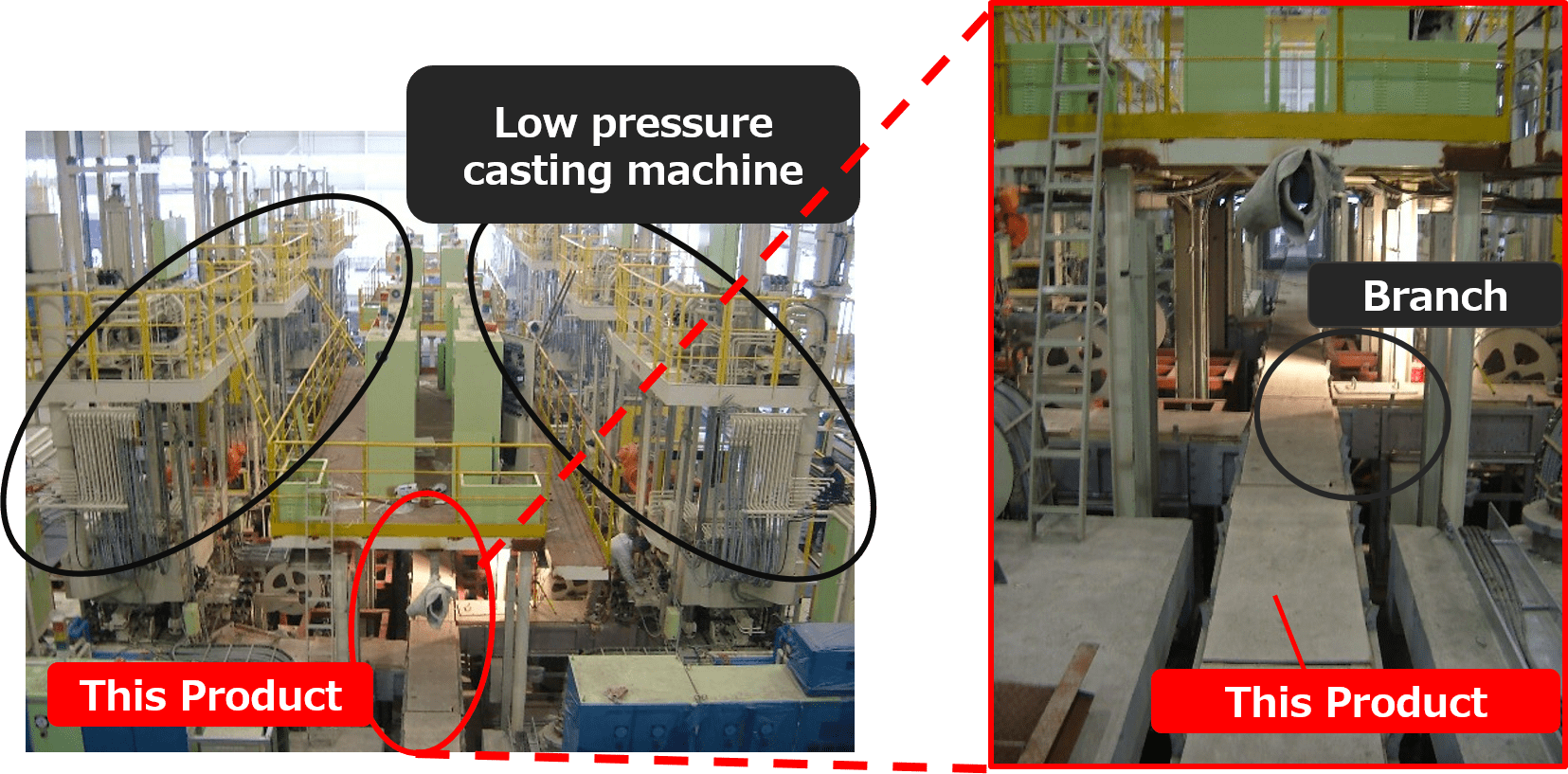